XXI. századi termékfejlesztés a Solid Edgeben, avagy hogyan számolhatunk le a sokszoros biztonsági tényezővel készült tervekkel
Melyik géptervező kolléga ne gondolkodott volna el még azon, hogy a tervezett konstrukciója vajon szilárdságtanilag megfelelő, vagy hogy az alkatrésze nincs esetleg túlbiztosítva szerkezetileg? Ezek olyan kérdések melyek, ha nincsenek megválaszolva költségnövekedést, illetve indokolatlan súlytöbbletet jelentenek. Azonban ezen kérdésekre már nem csak a drága, kis -és közép vállalkozások számára elérhetetlen végeselem modellező termékek tudják megadni a választ, hiszen manapság egyre több CAD szoftver kínál tervezési folyamatainkat szinkronban ellenőrző, integrált modulokat. A graphIT Kft. által forgalmazott Solid Edge felhasználói köre gyakran fordul hozzánk azzal a kérdéssel, hogy a szoftver által készített végeselem modell, mennyire hasonlítható össze a valóságban mért értékekkel, ezért szükségszerűnek tartottuk egy olyan projekt elindítását mely erre a kérdésre keresi a választ. A Budapesti Műszaki és Gazdaságtudományi Egyetemmel és a FREEDEE Kft-vel karöltve, egy diplomamunka keretein belül kísérletet tettünk arra, hogy gazdaságosság szempontjából összehasonlítsuk a hagyományos tervezést és gyártást a generatív tervezéssel és a 3D nyomtatással. Ezek alapján a Solid Edge-nek az alább látható moduljait vizsgáltuk meg tüzetesebben:
- Solid Edge Szimulációs modul
- Solid Edge Generatív tervezés modul
- Solid Edge 3D Nyomtatatás modul
Szimuláció és mechanikai vizsgálat összehasonlítása
A vizsgálati alanyként egy ipari robotkar megfogópofáját választottuk. Ugyanis az ipari robotok teherviselésének egyik kulcsfontosságú szerepe, hogy igyekezzünk minimalizálni a karra felszerelt részegységek tömegét, hiszen ezen eszközök tömegének összessége csökkenti a kar teherviselő képességét. Geometriai szempontból igyekeztünk olyan formát kialakítani, melyre releváns értékeket kaphatunk mind a szimulációs, mind a valós mechanikai vizsgálatokon.
A terheléses vizsgálatot rugalmas tartományban végeztük el, kihajlást és erőt mérve. Az alkatrészt CNC marással, a generatívan áttervezett változatát additív gyártással, végül DMLS 3D fémnyomtatással gyártottuk le. A vizsgálatok összehasonlíthatóságának érdekében fontos szempont volt, hogy a megfogópofa anyaga megtalálható legyen por és tömör rúd formájában is. Így a választott alapanyag az AlSi10Mg jelű alumínium ötvözet lett.
A megfogópofát felrögzítettük egy tervezett készülékre, majd befogtuk egy hidraulikus univerzális anyagvizsgáló gépbe, ahol egy nyomópofával ráálltunk a megfogó felső síkjára és ebben a pozícióban nulláztuk az erő és elmozdulás értékeket, így megkezdhettük a mérést. A mérési elrendezést a 1. ábra szemlélteti.
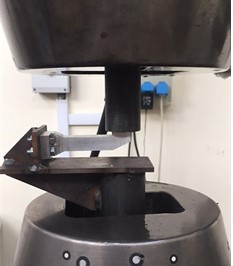
1. ábra Mechanikai vizsgálat
A mérés során a keresztfej elmozdulását és az erő értékeket regisztráltuk; a keresztfej sebessége 1 mm/perc volt. A vizsgálatot 1,2 mm keresztfej elmozdulásig végeztük.
A mechanikai vizsgálatot a Solid Edgeben és egy konkurens végeselem szoftverben szimulációs vizsgálattal is megismételtük. A kapott eredmények összehasonlítását (Solid Edge, Konkurens szoftver, CNC – mechanikai vizsgálat) az alább látható diagram szemlélteti (2.ábra).
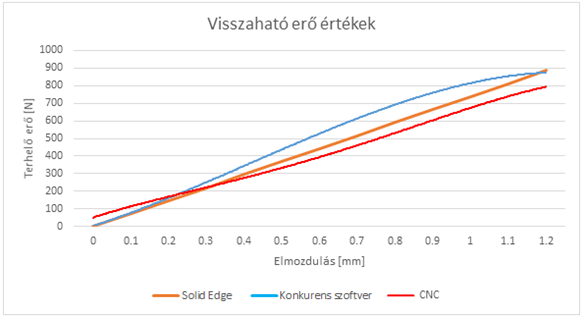
2. ábra Visszaható erő értékek az elmozdulás függvényében
A diagramról leolvasható, hogy a VEM szimulációk, közel azonos értékeket mutatnak, a vizsgálat első szakaszában, valamint a végső szakaszban a görbék egymásra simulnak, a közte lévő szakaszon pedig 10% alattiak az eltérések. A mechanikai vizsgálatot összehasonlítva a többi értékkel kb. 10 %-os eltérés látható. A végeselem modell és a mechanikai vizsgálat közötti csekély különbséget olyan tényezők befolyásolhatták, mint a készülék hegesztési varratainak figyelmen kívül hagyása, valamint a csavarkötések folyáshatára, ez esetben ugyanis a csavarkötés növelése geometriai korlátokba ütközött, míg a szimuláció során egységes testként helyettestettük őket.
Generatív tervezés és 3D nyomtatás
A geometriai optimalizálás és a 3D nyomtatás megjelenésével az ipar rengeteg új lehetFőséget kapott arra, hogy a termékeken további fejlesztéseket hajtson végre. Ezen innovációknak köszönhetően alkatrészeink kialakítása során már csak a képzelet szab határt. A diplomamunka folytatásában arra a kérdésre kerestük a választ, hogy ha alkatrészünket topológiai optimalizálásnak vetjük alá, akkor adott súlycsökkenés mellett meg tudjuk-e őrizni a merevségét a kijelölt munkatartományon belül. A hagyományos tervezési környezetben alkotott munkadarabunkkal való munkát generatív tervezés környezetben folytattuk.
Miután definiáltuk a használni kívánt modellt és a rendelkezésre álló térfogatot, a tervezés folyamán meghatároztuk azokat a régiókat, melyek változatlanok maradnak. Ilyen régiónak felelnek meg a furatok, rögzítési felületek, valamint a terhelt felületünk. A vizsgálat alatt alkalmazott erőnek, a VEM szimulációkból meghatározott visszaható erőt adtuk meg. Az eredeti tömeg 29 g, a vizsgálat során ennek a tömegnek a csökkentését végeztük el egy előre meghatározott értékkel, mely a mi esetünkben 30 % volt, tehát a cél 20 g elérése azonos mechanikai tulajdonságok megtartása mellett. Generatív tervezés során figyelembe kell venni a megmunkálás körülményeit, az anyag kitöltés és a réteg építési irányt, valamint a zárt üregek képződését. Anyag kitöltést tekintve 90%-ot adtunk meg, mely strukturált kitöltésnek felel meg. A vizsgálatok során kerültük a zárt üregek képződését, ugyanis a DMLS technológia miatt a por kiürítése az üregekből szerkezet gyengítéssel érhető el. A topológiai optimalizálás végeredményét a 3. ábra szemlélteti.
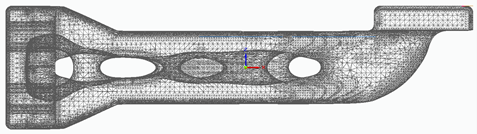
3. ábra Generatív terv háló modellje
A geometriailag optimalizált alkatrészünk legyártásához hamar sikerült megtalálnunk a megfelelő partnert. Választásunk a budapesti székhelyű FreeDee-re esett ugyanis Magyarországon egyedülállóként lefedik az additív gyártás teljes palettáját, illetve amellett, hogy rendkívül rövid gyártási határidővel tudnak dolgozni, nagy hangsúlyt fektetnek a minőségre és kiemelkedő ár-értékarányú szolgáltatást nyújtanak.
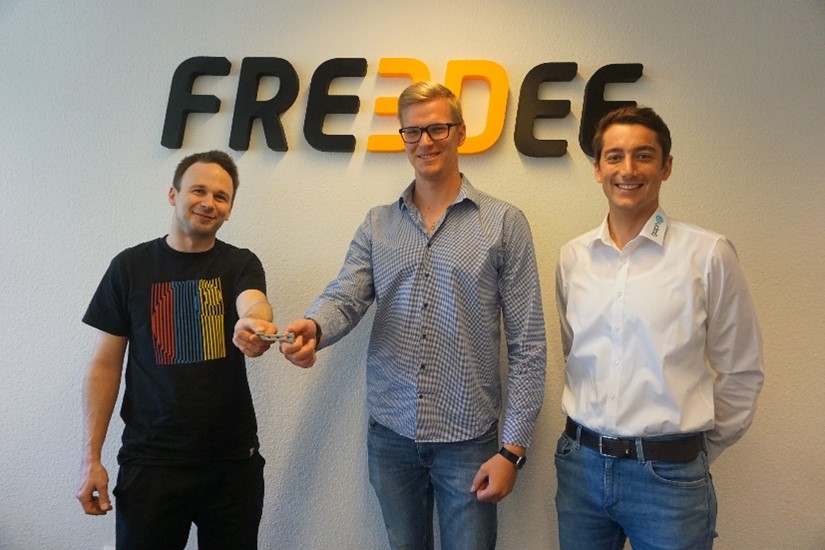
4. ábra Szabó Péter – FreeDee Kft; Mizser Dávid – BME; Szabó Dávid – graphIT Kft.
A projekt utolsó fázisaként a kinyomtatott munkadarabunkat ismét mechanikai vizsgálat alá vetettük. A mérés során a keresztfej elmozdulását és az erő értékeket regisztráltuk, a keresztfej sebessége 1 mm/perc volt. A vizsgálatot 1,2 mm keresztfej elmozdulásig végeztük, ahogy azt a szimulációk során is tettük. A 5. ábrán a CNC-vel gyártott munkadarab lehajlás értékei láthatóak a 3D nyomtatott termékkel összehasonlítva. Jól látható, hogy a munkatartományban (150 N körül) a mért értékek nem ütnek el egymástól nagy mértékben, vagyis a 30%-os tömegcsökkentés nem ment a termék merevségének kárára.

5. ábra Visszaható erő értékek az elmozdulás függvényében mind CNC mind pedig additív Manufacturing gyártott alkatrész esetén
Összeségében elmondható, hogy mind a Solid Edge szimulációs modulja, mind pedig a generatív tervezés modulja, nagyban segítik a mérnöki munkavégzést és a termékfejlesztés folyamatát, csökkentve a tervezési költségeket, valamint a hulladék és a felhasznált alapanyag mennyiségét.